Cold storage
The closed cold chain from raw material to product ensures that the full freshness and quality of the hops is maintained.
In particular, the alpha acids contained in hops and of high brewing value are thus prevented from degrading.
Both the raw hops and the products produced are taken to our cold stores for storage. We currently have a storage capacity of approx. 9,000 tons of raw hops, which corresponds to approx. 150,000 rectangular bales and more than 23,700 pallet spaces for finished products. The temperature in all cold stores is approx. 3°C. Both the temperature and the humidity of these rooms are permanently monitored and documented.
After harvesting, the raw hops are delivered in the form of rectangular bales of approx. 60 kg each. Packages belonging together, so-called lots, are stored together and are clearly identifiable throughout. During storage, the batches are checked for completeness, correctness, external condition and moisture content. Hops without defects are immediately transferred to cold storage. Finished hop products are also stored in cold storage immediately after processing until collection.
A professional warehouse management system supports logistics and enables inventory management.
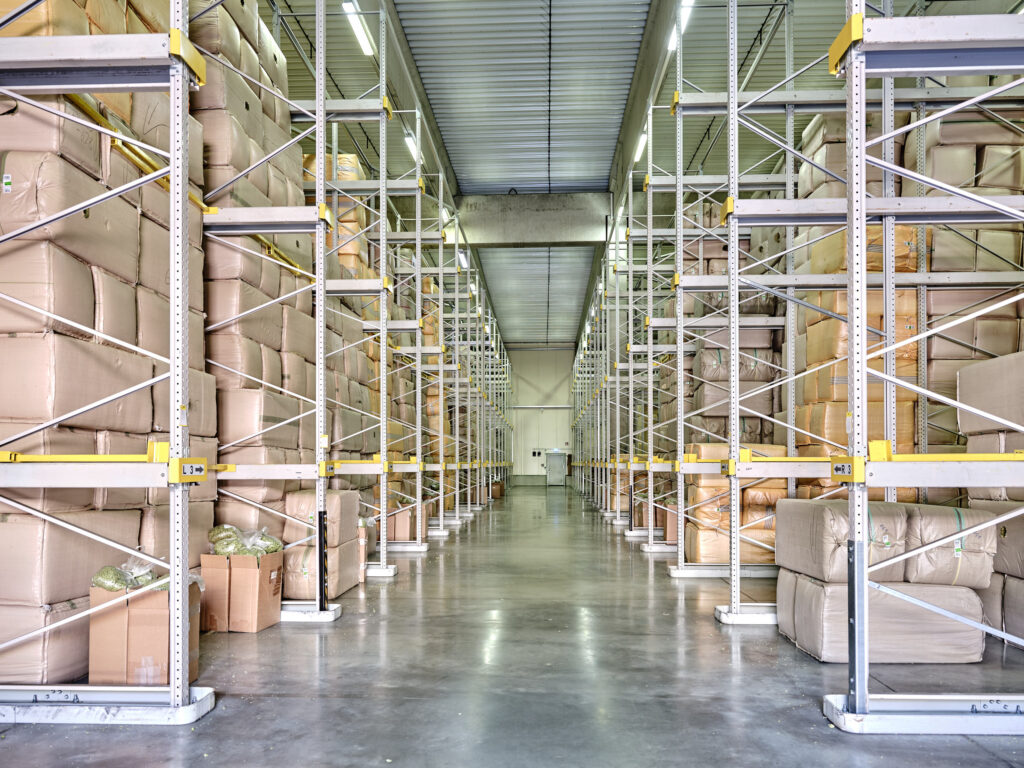
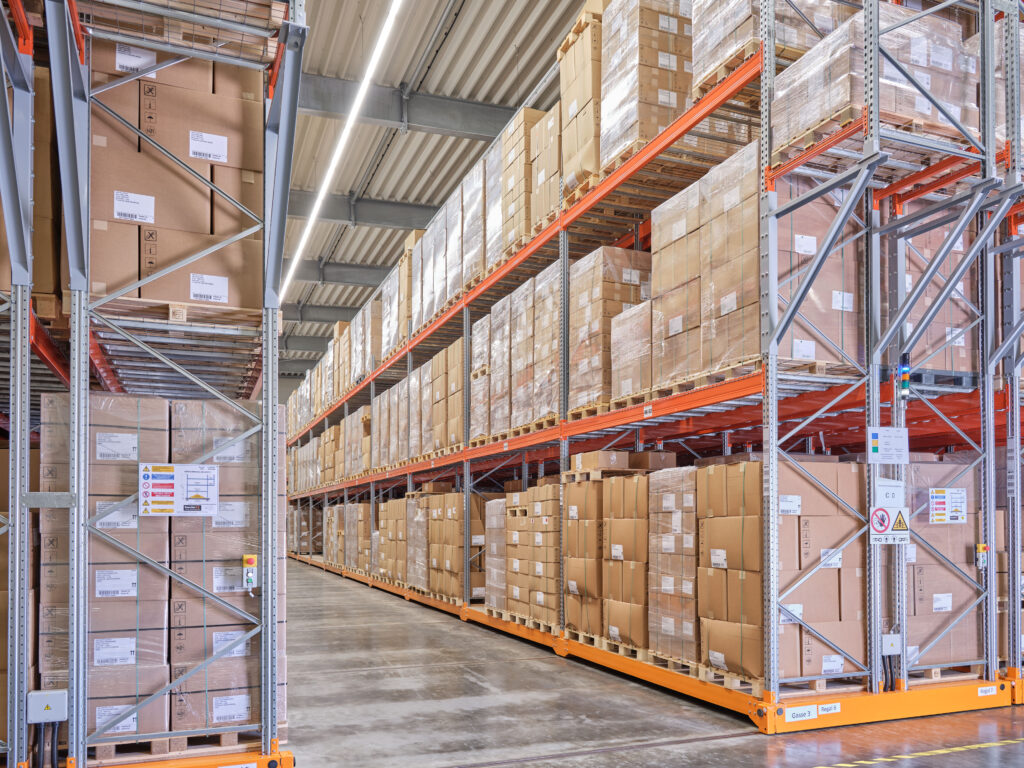
Quality assurance
For safe and accurate description of all manufactured hop products.
We rely on the decades of experience and knowledge of our modern equipped quality assurance. Analytics is supported by an up-to-date Laboratory Information Management System (LIMS), thus we offer a high level of digitalization and data management.
The focal points of the laboratory can be divided into two areas:
During processing, the hop powder (type 45) and the finished pellets (type 90 and type 45) are routinely analyzed for alpha acid content according to the desired analytical methods. This tests the entire processing operation for homogeneity and accuracy. The alpha standardization and the product markings are controlled directly and promptly depending on the laboratory results.
The control of the water content to ensure correct drying is also subject to constant monitoring.
The various extract fractions also fall within the analytical remit of quality assurance. Alpha acid, isoalpha acid and oil content play a decisive role here.
For optimum yield control, the hop spent grains from enrichment and extraction are permanently monitored for residual alpha content.
Our laboratory is staffed 24 hours during the entire processing time.
Raw hops
At the beginning of the hop harvest, several thousand samples are analyzed for alpha content as part of our neutral quality assessment. In addition, large-scale screening of many relevant hop varieties for important brewing parameters also takes place regularly during this period. This gives our customers the opportunity to select hop batches for subsequent processing orders in line with product requirements.
Aroma analytics
In addition to the extraction and quantification of the oil content in hops and hop products, we offer a comprehensive determination of individual hop oil components. Especially terpene-like hydrocarbons, ketones and esters play an important role in the aroma profile of hops.
Plant protection products (PPPs)
The control of chemical crop protection plays an enormous role for hop marketers. They are responsible for ensuring that only marketable hop lots are used for processing. To this end, we determine the legally specified maximum levels using our most sophisticated and sensitive equipment (GC- and LC-MS/MS). Currently, the two multi-methods cover a total of around 140 individual substances.
Element contents
Both through targeted application in crop protection and through certain process steps in pre-isomerization, contents of individual metals (e.g. copper or magnesium) must be monitored and evaluated. For this purpose, our quality assurance department has a modern ICP-OES spectrometer, which can be used to determine a large number of elements simultaneously. The entire product spectrum can be analyzed.
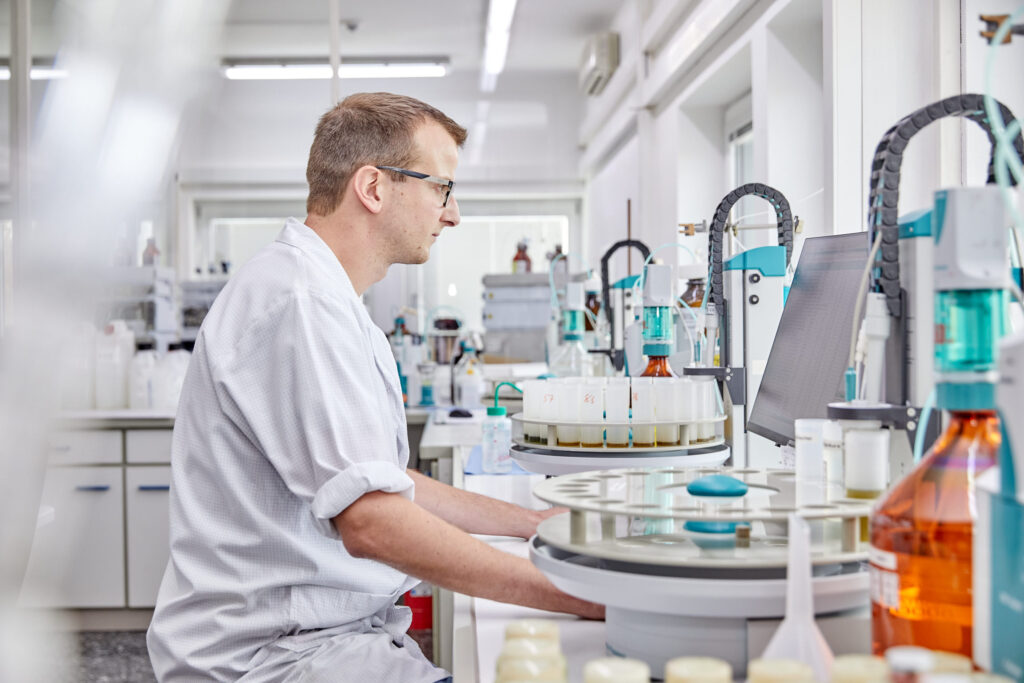
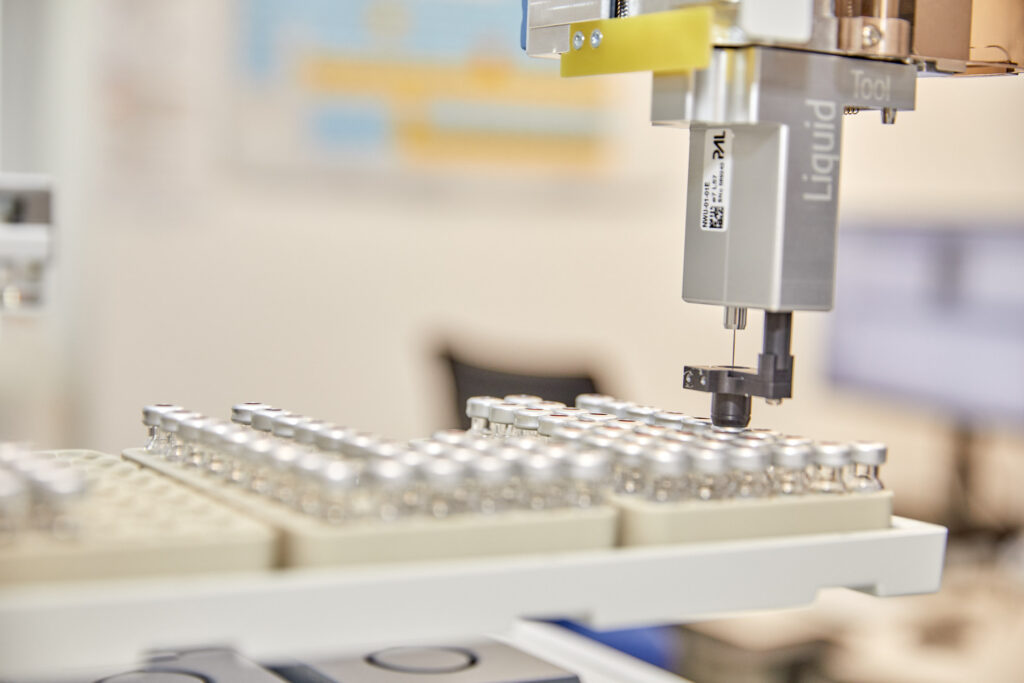
Pelletizing
The hops are processed into pellets in defined processing orders.
Through targeted production planning, the various processing orders are processed on our different production lines. Our goal is to manufacture products with the highest quality.
For non-enriched pellets (type 90), the pressed raw hops are first loosened and homogenized. It is then post-dried, freed from heavy material and foreign particles, and milled. The resulting hop powder is fed into a mixer, where it is homogenized again and then processed into pellets in the pellet mills. Interim storage in silos is followed by immediate filling of the pellets.
In the production of enriched pellets (type 45) we have additional processing steps. Before the hops enter the blenders, they are milled and sieved in the deep-freeze area at approx. -36 °C. The hops are then processed in the blender. Due to the extremely low temperature, a complete crystallization of the contained resins, consequently also of the lupulin, takes place. In this way, the entire ground material can be separated into less desirable components such as cone leaves, stems, and stalks (coarse material) and the desirable lupulin of high brewing value (fine material) by means of vibrating centrifuges. Standardization to a defined α-acid content is then achieved by controlled merging of an appropriate quantity of fine and coarse material in the mixer. The further process is similar to that of the non-enriched pellets.
In the case of isomerized hop pellets (ISO), the process is in accordance with Type 90 or Type 45. In addition, a magnesium oxide dosage is carried out during the powder mixing process and subsequent storage of the pellets in a heat zone for a defined period of time.
Production flow pelletizing (CREATE INFOGRAPH?!)
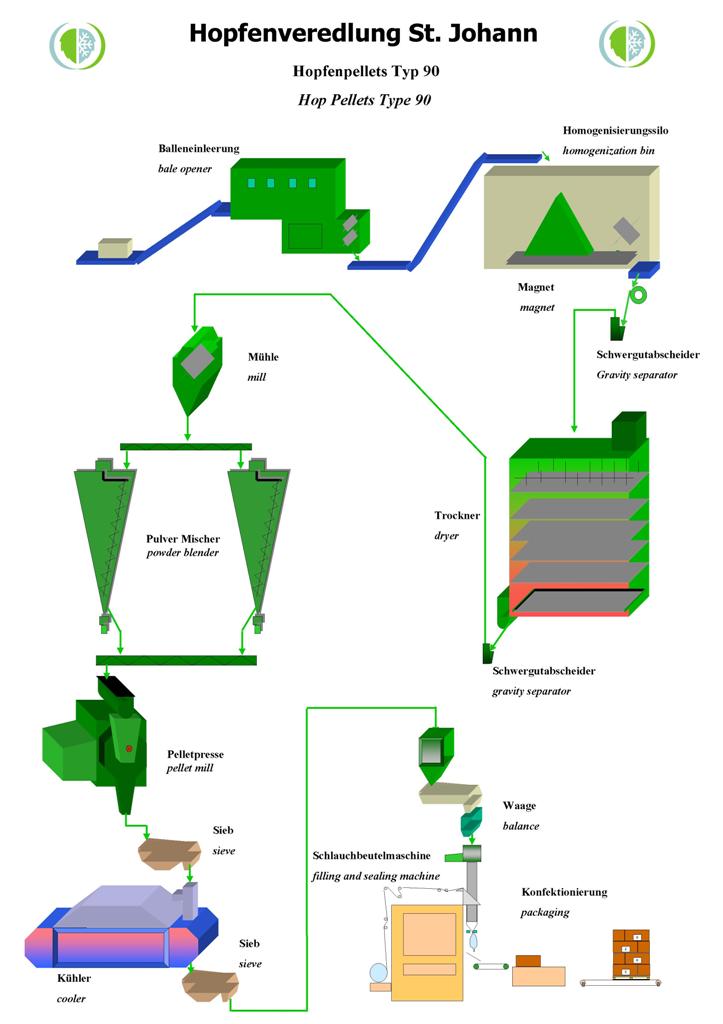
Extraction
Our hop extracts are produced in the world's largest and most modern hop extraction plant.
With 8 extractors, high-quality hop extract is produced in a gentle manner. The Extraxt is stored in 22 tanks in a highly flexible manner and standardized.
The raw hops are pre-pelletized in a special production plant. These hop pellets are filled into an extraction container (=extractor). To extract the ingredients from the hops, we use the biogenic solvent carbon dioxide, in short CO2. With the aid of a pump, the liquid CO2 is compressed to the extraction pressure of up to 500 bar. This produces supercritical CO2, which flows through the hops in the extractor and dissolves the brewing-relevant substances. Subsequently, by lowering the pressure in the separator, the CO2 and extract are separated from each other again. By stepwise regulation of various parameters, two different fractions, oil-reduced and oil-enriched extract, can be produced.
The extracts are pumped from the separator to the tank farm and prepared for filling.
The CO2 is liquefied again in a heat exchanger and returned to the cycle.
For the production of Isomerized Kettle Extract we have a separate production plant.
Production process CO2 extraction (CREATE INFOGRAPH?!)
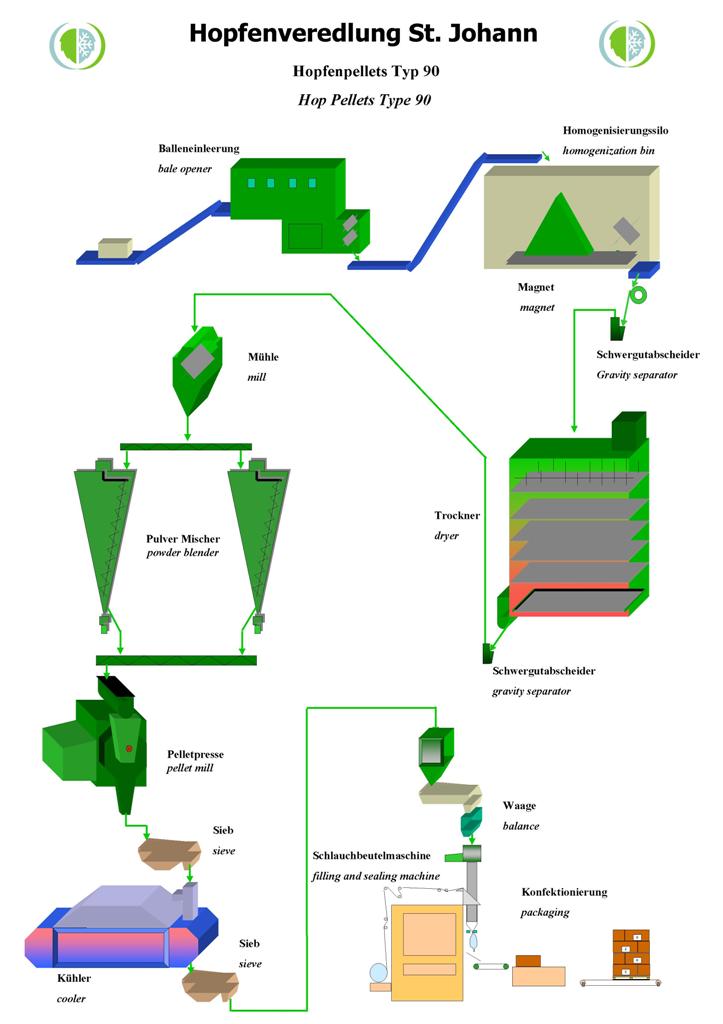
Packing & Logistics
The packaging of finished products is carried out individually and according to customer requirements.
Our own logistics department guarantees careful and smooth loading of the finished products.
Filling is carried out according to the customer's requirements, and the bag sizes can be adjusted individually. The hop pellets are filled into bags using calibrated scales and then packed into cartons.
To meet the required packaging sizes, we have five different filling lines, so it is possible to fill bags from 300 g to 20 kg.
The pellets are packaged and labeled in special aluminum composite films using form fill and seal machines. To avoid damage to the product by oxygen, the films are enriched with inert gas and sealed. An inspection of the sealing edges and weights is carried out permanently. The finished bags are packed into the appropriate cartons, labeled and sealed.
Alternatively, it is possible to fill the pellets in large cartons of 90 and 140 kg. Here, the carton is lined with a prefabricated sealed-edge bag (aluminum composite) and filled with the pellets, also enriched with inert gas, sealed and closed. The cartons are stacked on pallets and secured against slipping with strapping bands. At the customer's request, the finished pallet is additionally wrapped with stretch film.
The finished product range certified by seal officials of the municipality and transported to the cold storage.
Extract filling is carried out individually according to customer requirements. Filling via calibrated scales is possible in cans, plastic containers and disposable drums.
The cans can be filled with 100 g to 3 kg of extract. All cans are automatically checked for integrity before filling and sorted out if damaged. The extract runs through 10 filling stations simultaneously into the designated cans, followed by a check weighing. The cans are closed with a lid, labeled with a laser and then packed in cartons. After the cartons have been sealed, labeling and strapping take place.
In addition, plastic containers (up to max. 18 kg) and disposable drums (up to max. 200 kg) are available in two sizes each for extract filling.
The filled extracts are packed on pallets and secured with strapping bands.
At the customer's request, the product pallets are additionally wrapped with stretch film.
The finished product certified by seal officials of the municipality and then stored.
Product shipment is organized by our customers and handled by our logistics staff. Loading takes place on the load carrier specified by the customer.
The load is secured in accordance with the applicable legislation.